RS 2(3) Netting Warp Knitting Machine
Single-Bar Raschel Machines: The Ideal Solution for Net Production
Single-bar Raschel machines provide an innovative and highly efficient solution for producing various types of textile nets, including agricultural, safety,
and fishing nets. These nets serve a wide range of applications, with one of their primary functions being protection against adverse weather conditions. In
these cases, they must withstand constant exposure to varying climatic effects. The advanced warp knitting technology integrated into single-bar Raschel
machines offers unmatched possibilities for net production, surpassing any other manufacturing method in versatility and performance.
Key Factors Influencing Net Characteristics
- Lapping technique
- Number of guide bars
- Machine gauge
- Yarn threading arrangement
- Stitch density
- Type of yarn used
By adjusting these parameters, manufacturers can tailor the net’s properties to meet diverse end-use requirements, such as:
- Sun protection factor: Controlling the level of shade provided
- Wind permeability: Adjusting airflow resistance
- Opacity: Regulating visibility through the net
- Stability and elasticity: Modifying flexibility in lengthwise and crosswise directions
Fundamental Lapping Constructions for Net Production
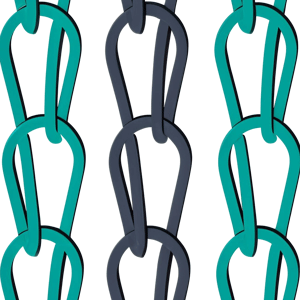
1. Pillar Stitch
The pillar stitch construction is the foundation for net manufacturing and the most commonly used lapping technique. It ensures the
required lengthwise strength and stability, making it essential for net durability. However, to create a functional textile substrate,
the pillar stitch must be combined with an inlay lapping or other complementary structures.
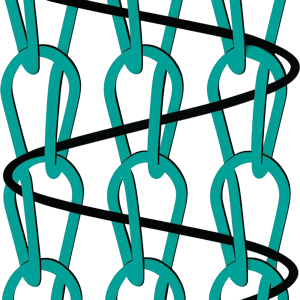
2. Inlay (Weft)
While an inlay structure alone cannot form a textile substrate, it plays a crucial role in crosswise stability. By
interconnecting two, three, or more stitch wales, the inlay enhances the fabric’s resistance to lateral forces. Generally, the more wales joined
together in an underlap, the more stable and resilient the net becomes.
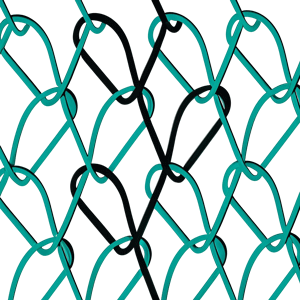
3. Tricot Lapping
Tricot lapping is achieved by the sideways shogging of the guide bar relative to the adjacent needle. When used without additional
guide bars, it results in a highly elastic fabric. Due to its inherent high elasticity in both lengthwise and
crosswise directions, tricot lapping is rarely used in net manufacturing—unless combined with additional guide bars to improve stability.
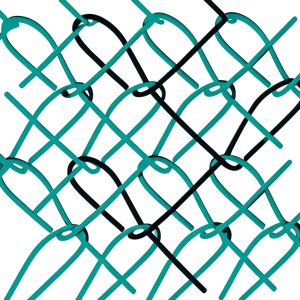
4. 2 x 1 Lapping
Similar to tricot lapping, the 2 x 1 lapping joins adjacent wales. However, instead of forming the next loop on the immediately
adjacent needle, it is created on the next-but-one needle. This principle applies to most stitch lappings, with the exception of pillar stitch
constructions.
Designing Nets with Varying Shapes and Sizes
A crucial aspect of net production is the ability to create net openings in different sizes and shapes, which is achieved by modifying key
factors such as:
- Machine gauge
- Lapping construction
- Stitch density
Additionally, the yarn threading arrangement plays a decisive role. Unlike standard configurations, the threading pattern does not always
have to align perfectly with the machine gauge. To maximize flexibility, threading variations such as 1 in, 1 out or
1 in, 2 out are frequently applied. This allows manufacturers to produce a diverse range of nets on a single machine, minimizing downtime
and eliminating the need for frequent, time-consuming changeovers.
Conclusion: Maximum Efficiency with Warp Knitting Technology
Single-bar Raschel machines offer unrivaled efficiency and adaptability for textile net production, ensuring the highest standards in
strength, stability, and design versatility. By leveraging advanced warp knitting technology, manufacturers can seamlessly customize net properties to meet
a vast range of industrial and protective applications—setting new benchmarks in net manufacturing excellence.
GrandStar® Warp Knitting Machine Specifications
Working Width Options:
- 4597mm (181″)
- 5207mm (205″)
- 6807mm (268″)
- 7188mm (283″)
- 8509mm (335″)
- 10490mm (413″)
- 12776mm (503″)
Gauge Options:
- E2, E3, E4, E5, E6, E8
Knitting Elements:
- Needle Bar: 1 single needle bar utilizing latch needles.
- Slider Bar: 1 slider bar with plate slider units.
- Knockover Bar: 1 knock over comb bar featuring knock-over units.
- Guide Bars: 2(3) guide bars with precision-engineered guide units.
- Material: magnalium bars for superior strength and reduced vibration.
Yarn Feeding System:
- Warp Beam Support: 2(3) × 812mm (32″) (free-standing)
- Yarn Feeding Creel: Working from a creel
- FTL: Film Cutting and strctching device
GrandStar® Control System:
The GrandStar COMMAND SYSTEM provides an intuitive operator interface, allowing seamless machine configuration and precise electronic function control.
Integrated Monitoring Systems:
- Integrated Laserstop: Advanced real-time monitoring system.
Yarn Let-Off System:
Each warp beam position features an electronically controlled yarn let-off drive for precise tension regulation.
Fabric Take-Up Mechanism:
Equipped with an electronically regulated fabric take-up system driven by a high-precision geared motor.
Batching Device:
A separate floor-standing cloth rolling device ensures smooth fabric batching.
Pattern Drive System:
- Standard: N-drive with three pattern discs and integrated tempi change gear.
- Optional: EL-drive with electronically controlled motors, allowing guide bars to shog up to 50mm (optional extension to 80mm).
Electrical Specifications:
- Drive System: Speed-regulated drive with a total connected load of 25 kVA.
- Voltage: 380V ± 10%, three-phase power supply.
- Main Power Cord: Minimum 4mm² three-phase four-core cable, ground wire no less than 6mm².
Oil Supply System:
Advanced oil/water heat exchanger ensures optimal performance.
Operating Environment:
- Temperature: 25°C ± 6°C
- Humidity: 65% ± 10%
- Floor Pressure: 2000-4000 kg/m²
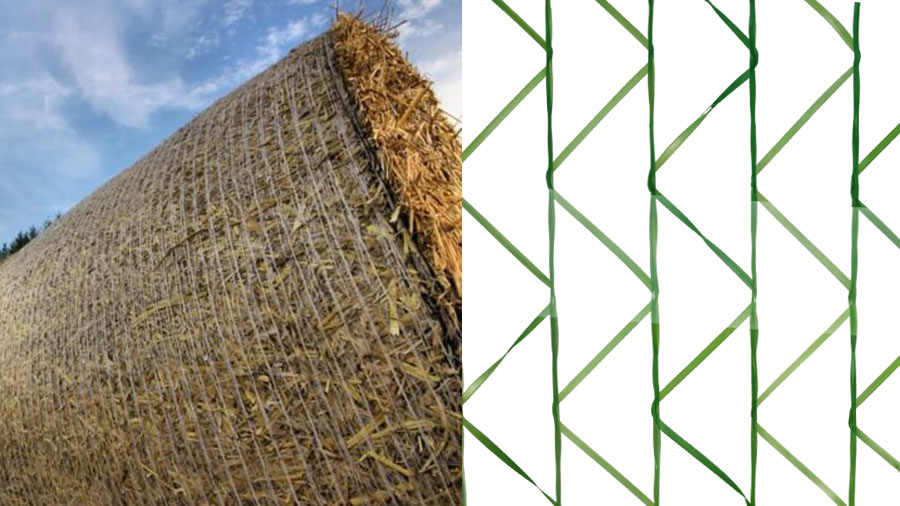
Lightweight polyethylene nets designed for securing hay and straw bales, as well as stabilizing pallets for transport. Produced with a specialized pillar stitch/inlay technique, these nets feature widely spaced wales and a low needle density for optimal performance. The batching system ensures tightly compressed rolls with extended running lengths, maximizing efficiency and storage.
Widely used in warm climates, warp-knitted shade nets protect crops and greenhouses from intense sunlight, preventing dehydration and ensuring optimal growth conditions. They also enhance air circulation, reducing heat buildup for a more stable environment.
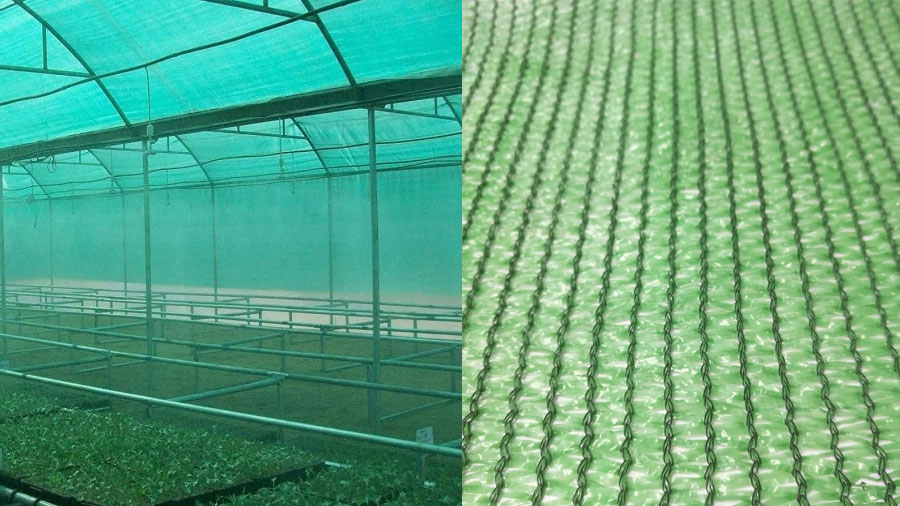
Waterproof ProtectionEach machine is meticulously sealed with sea-safe packaging, providing robust defense against moisture and water damage throughout transit. |
International Export-Standard Wooden CasesOur high-strength composite wooden cases fully comply with global export regulations, ensuring optimal protection and stability during transportation. |
Efficient & Reliable LogisticsFrom careful handling at our facility to expert container loading at the port, every step of the shipping process is managed with precision to guarantee safe and timely delivery. |