KSJ 4/1-T (EL) Tricot Terry Towel With Jacquard
Revolutionizing Terry Towel Production with Warp Knitting Technology
Unmatched Efficiency & Sustainability in Terry Towel Manufacturing
The Terry Warp Knitting Machine is the ideal solution for producing high-quality microfiber terry towels, widely used for cleaning and personal care applications. Compared to traditional loom-based terry machines, warp knitting technology offers significantly higher productivity, reduced material waste, and a more environmentally friendly production process. By eliminating the excessive water and energy consumption associated with conventional weaving methods, this innovative approach sets a new benchmark in sustainable textile manufacturing.
Expanding Product Applications with Superior Versatility
The Microfiber Towel Warp Knitting Machine is designed to create an extensive range of terry towel products, including:
- Cleaning microfiber towels
- Luxury bathrobes
- Premium beach towels
- High-absorbency hotel towels
This versatility allows manufacturers to meet the growing demand for durable, soft, and absorbent textiles across various industries.
KSJ 4/1-T: Advanced Jacquard-Patterned Terry Towel Machine
For businesses seeking enhanced design flexibility, the KSJ 4/1-T offers state-of-the-art capabilities. As a jacquard-patterned terry towel machine, it is equipped with an advanced piezo-jacquard system, allowing intricate and customized pattern designs with exceptional precision.
Engineered specifically for patterned microfiber terry towel textiles, the KSJ 4/1-T delivers outstanding production efficiency while maintaining superior fabric quality. Its application range includes:
- Cleaning terry towels
- Luxury bathrobes
- Designer beach towels
- High-end hotel towels
Why Choose Warp Knitting Technology for Terry Towels?
- Unrivaled Production Speed – Significantly higher output compared to traditional weaving methods
- Eco-Friendly & Resource-Efficient – Lower energy consumption and minimal water usage
- Enhanced Design Flexibility – Seamlessly integrates jacquard patterning for premium textile customization
- Versatile Application Scope – Ideal for personal, commercial, and industrial microfiber towel markets
By integrating the KSJ 4/1-T Terry Towel Machine into your production line, you gain access to cutting-edge technology that enhances efficiency, quality, and sustainability in towel manufacturing.
Upgrade your production capabilities with warp knitting technology and lead the future of high-performance terry towel textiles.
Technical Specifications
Working Width
- 4727 mm (186″)
- 5588 mm (220″)
- 6146 mm (242″)
- 7112 mm (280″)
Working Gauge
E24
Bars & Knitting Elements
- Independent needle bar equipped with compound needles
- Slider bar featuring plate slider units (1/2″)
- Sinker bar integrated with compound sinker units
- Pile bar equipped with pile sinkers
- Three guide bars fitted with precision-engineered guide units
- Two Piezo Jacquard guide bars (1 Group)
- All bars are constructed from high-strength carbon-fibre for enhanced durability and stability
Warp Beam Support
- Standard Configuration: 4 × 812 mm (32″) free-standing beams
- Optional Configuration: 4 × 1016 mm (40″) free-standing beams
GrandStar® Control System
The GrandStar COMMAND SYSTEM delivers an intuitive operator interface, enabling seamless configuration, real-time monitoring, and precision control of all electronic functions to optimize machine performance.
Integrated Monitoring Systems
Integrated Laserstop Technology: Advanced real-time monitoring system for immediate detection and response to potential operational discrepancies.
Yarn Let-Off System (EBC)
- Electronically controlled yarn delivery system, driven by a precision-engineered geared motor
- Sequential let-off device included as a standard feature
Pattern Drive System
EL-Drive powered by high-precision servo motors
Supports guide bar shogging up to 50mm (optionally expandable to 80mm)
Fabric Take-Up System
Electronically regulated fabric take-up system
Four-roller continuous take-up execution, driven by a geared motor for precision and consistency
Batching System
- Central drive batching mechanism
- Equipped with a sliding clutch
- Maximum batch diameter: 736 mm (29 inches)
Electrical System
- Speed-regulated drive system with a total power consumption of 25 kVA
- Operating voltage: 380V ± 10%, three-phase power supply
- Main power cable requirement: minimum 4mm² three-phase four-core cable, with an additional ground wire of no less than 6mm²
Oil Supply System
- Advanced lubrication system with pressure-regulated crankshaft lubrication
- Integrated oil filtration with dirt-monitoring system for extended service life
- Cooling Options:
- Standard: Air heat exchanger for optimal temperature regulation
- Optional: Oil/water heat exchanger for enhanced thermal management
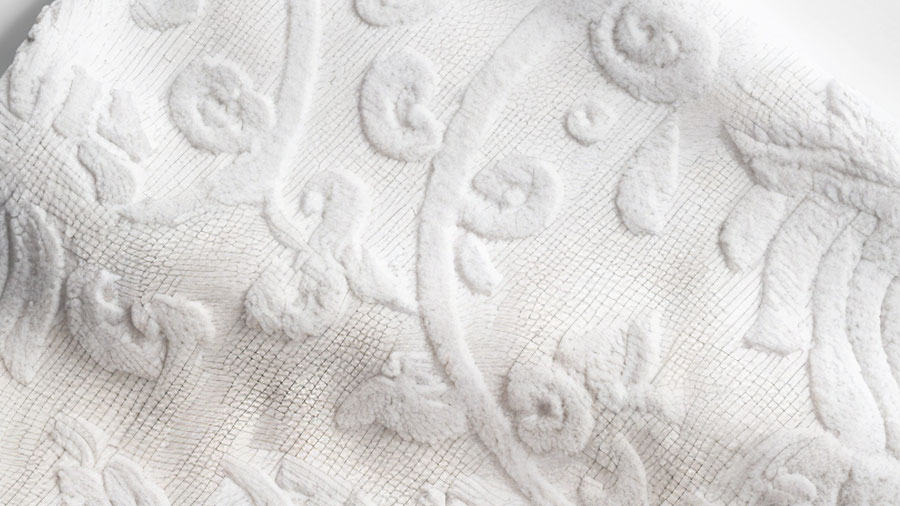
Rear jacquard bar enhances pattern versatility, enabling intricate designs like images and characters..
Enhance fabric texture with the KSJ Jacquard’s advanced 3D effects. Create raised ribs, corded patterns, and structured surfaces that bring depth and dimension to your designs. Perfect for fashion and upholstery, these fabrics captivate both visually and to the touch.
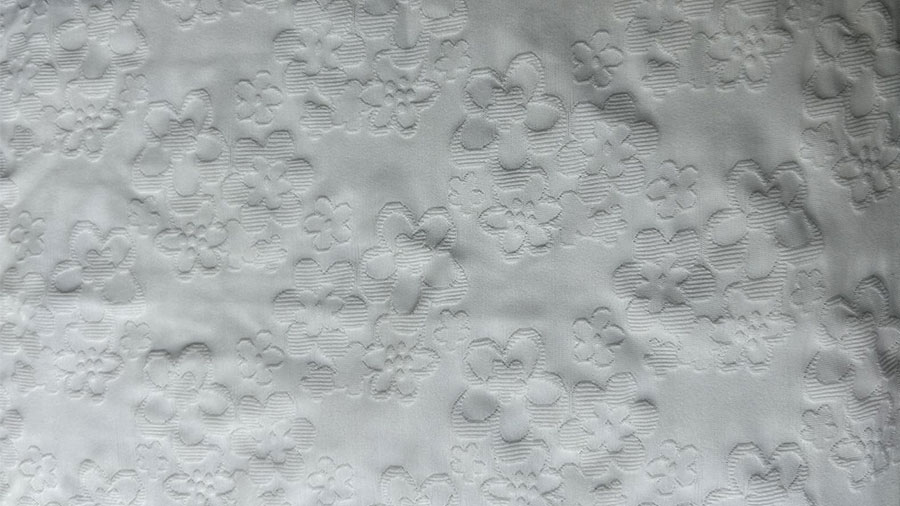
Waterproof ProtectionEach machine is meticulously sealed with sea-safe packaging, providing robust defense against moisture and water damage throughout transit. |
International Export-Standard Wooden CasesOur high-strength composite wooden cases fully comply with global export regulations, ensuring optimal protection and stability during transportation. |
Efficient & Reliable LogisticsFrom careful handling at our facility to expert container loading at the port, every step of the shipping process is managed with precision to guarantee safe and timely delivery. |