HKS-4-T (EL) Tricot Machine For Terry Towel
Revolutionizing Terry Towel Production with Warp Knitting Technology
Innovative Solutions for High-Performance Terry Towel Fabrics
The GS-HKS4-T warp knitting machine is designed to set new industry benchmarks in terry towel production, offering
unmatched efficiency, flexibility, and fabric quality. Engineered specifically for
staple fibre and filament yarn processing, this high-performance machine meets the evolving demands of the textile market.
Expanding Market Opportunities with Microfiber Innovation
Traditionally, terry towels were exclusively made from cotton. However, the introduction of PE/PA microfiber has transformed the industry,
providing a superior alternative for towel production. This shift has opened up new possibilities for warp knitting technology, offering
enhanced softness, durability, and absorption efficiency. The GS-HKS4-T is optimized to harness the full potential of
microfiber fabrics, making it an essential solution for modern textile manufacturers.
Key Advantages of the GS-HKS4-T
-
✅ Optimized for Staple Fibre and Filament Yarn
Designed for versatile material compatibility, ensuring high-quality fabric output across different yarn types.
-
✅ Integrated Online Brushing Device
A built-in brushing system guarantees even loop formation, enhancing the plush texture and uniformity of the fabric.
-
✅ High Performance & Exceptional Flexibility
Combining speed, precision, and adaptability, this machine excels in both high-volume production and intricate fabric designs.
-
✅ Long Pattern Design Capability
The EL-drive system enables extended pattern configurations, unlocking greater design possibilities for premium towel production.
-
✅ Enhanced Creativity with the Jacquard System
An advanced Jacquard system broadens pattern versatility, allowing manufacturers to produce unique and intricate towel textures.
-
✅ Uncompromising Operational Reliability
Built with cutting-edge engineering and durable components, ensuring consistent performance and minimal downtime.
-
✅ Extended Machine Service Life
A robust machine structure and high-quality components guarantee long-term reliability, reducing maintenance costs and
maximizing production efficiency.
Setting New Standards in Terry Towel Manufacturing
With its advanced features, superior design, and market-oriented innovation, the GS-HKS4-T is an ideal choice for
manufacturers looking to expand their product range while maintaining high efficiency and fabric excellence. By leveraging the benefits of
warp knitting technology, this machine enables businesses to stay ahead in the competitive terry towel industry.
Technical Specifications
Working Width
- 4727 mm (186″)
- 5588 mm (220″)
- 6146 mm (242″)
- 7112 mm (280″)
Working Gauge
E24
Bars & Knitting Elements
- Independent needle bar equipped with compound needles
- Slider bar featuring plate slider units (1/2″)
- Sinker bar integrated with compound sinker units
- Pile bar equipped with pile sinkers
- Four guide bars fitted with precision-engineered guide units
- All bars are constructed from high-strength carbon-fibre for enhanced durability and stability
Warp Beam Support
- Standard Configuration: 4 × 812 mm (32″) free-standing beams
- Optional Configuration: 4 × 1016 mm (40″) free-standing beams
GrandStar® Control System
The GrandStar COMMAND SYSTEM delivers an intuitive operator interface, enabling seamless configuration, real-time monitoring, and precision control of all electronic functions to optimize machine performance.
Integrated Monitoring Systems
Integrated Laserstop Technology: Advanced real-time monitoring system for immediate detection and response to potential operational discrepancies.
Yarn Let-Off System (EBC)
- Electronically controlled yarn delivery system, driven by a precision-engineered geared motor
- Sequential let-off device included as a standard feature
Pattern Drive System
EL-Drive powered by high-precision servo motors
Supports guide bar shogging up to 50mm (optionally expandable to 80mm)
Fabric Take-Up System
Electronically regulated fabric take-up system
Four-roller continuous take-up execution, driven by a geared motor for precision and consistency
Batching System
- Central drive batching mechanism
- Equipped with a sliding clutch
- Maximum batch diameter: 736 mm (29 inches)
Electrical System
- Speed-regulated drive system with a total power consumption of 25 kVA
- Operating voltage: 380V ± 10%, three-phase power supply
- Main power cable requirement: minimum 4mm² three-phase four-core cable, with an additional ground wire of no less than 6mm²
Oil Supply System
- Advanced lubrication system with pressure-regulated crankshaft lubrication
- Integrated oil filtration with dirt-monitoring system for extended service life
- Cooling Options:
- Standard: Air heat exchanger for optimal temperature regulation
- Optional: Oil/water heat exchanger for enhanced thermal management
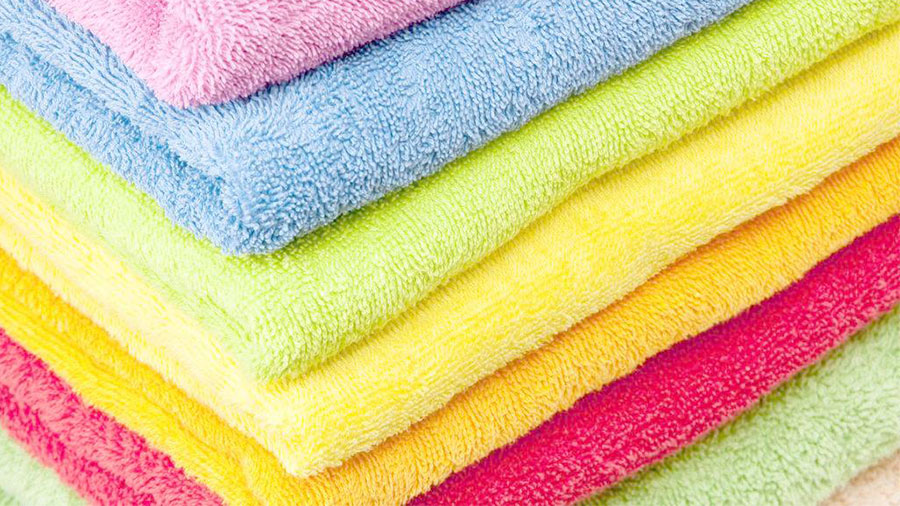
Warp Knitting Terry Cloth features a looped pile construction, ensuring high absorbency and excellent moisture-wicking—perfect for fast-drying applications.
Warp knitting terry cloth is ideal for towels, bathrobes, and cleaning products. Polyester terry cloth, known for its durability and resistance to wrinkles and stains, is widely used in industrial and outdoor applications.
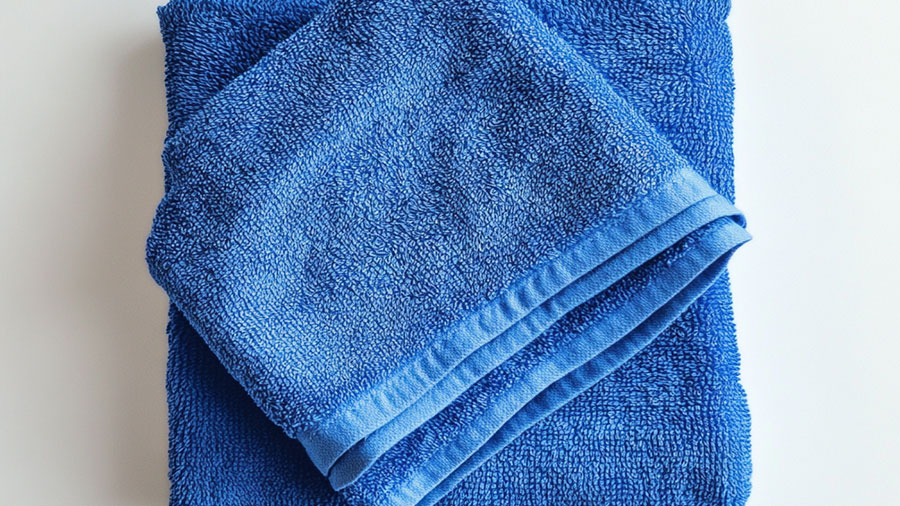
Waterproof ProtectionEach machine is meticulously sealed with sea-safe packaging, providing robust defense against moisture and water damage throughout transit. |
International Export-Standard Wooden CasesOur high-strength composite wooden cases fully comply with global export regulations, ensuring optimal protection and stability during transportation. |
Efficient & Reliable LogisticsFrom careful handling at our facility to expert container loading at the port, every step of the shipping process is managed with precision to guarantee safe and timely delivery. |